Week 16
Wildcard Week
Assignment
Individual
• Design and produce something with a digital fabrication process not covered in another assignment, documenting the requirements that your assignment meets, and including everything necessary to reproduce it. Possibilities include (but are not limited to) composites, textiles, biotechnology, robotics, and cooking.
Leather
Kenya Leather Industry - Diagnosis, Strategy and Action Plan
In this week assignment I wanted to try out something with leather.
In 2014, Kenya’s Ministry of Industrialization requested technical assistance from the World Bank to conduct competitiveness assessments and develop competitiveness strategies for four key industries: textiles and apparel, food processing, furniture, and leather and leather products. The Ministry selected these four industry sectors for serious consideration as priority sectors for industrial development and job creation in Kenya. In the context of Kenya’s long-term vision to become an industrialized middle-income country by 2030, its leather and leather products sector offers an important opportunity for industrialization and diversification of exports. However, value addition in the leather sector has been minimal, and most of Kenya’s exports have been in the form of unprocessed, raw hides and skins. The leather sector can contribute to economic growth through expanding exports of both semi-processed and finished leather goods. The development of the sector involves improving the raw material base (especially the quality of hides and skins), boosting the tanning subsector, producing leather goods, and marketing.
Reference: http://www.industrialization.go.keWhat is leather?
Leather is a durable and flexible material created by tanning animal rawhides, mostly cattle hide. It can be produced at manufacturing scales ranging from cottage industry to heavy industry. Leather is used to make various goods, including clothing (especially footwear), in bookbinding, and as a furniture covering. It is produced in a wide variety of types and styles, decorated by a wide range of techniques. The leather manufacturing process is divided into three fundamental subprocesses: preparatory stages, tanning, and crusting. A further subprocess, surface coating, can be added into the leather process sequence, but not all leathers receive surface treatment.
Types of Leather
i) Top grain - Top grain is the second highest grade of leather. Usually, to obtain top grain leather, the top layer of skin from blemished hides is split. The surface is sanded to get rid of inherent imperfections. Pigmentation or staining gives the leather an attractive look.
ii) Full grain - Full grain leather comes from the top layer of the hide. It includes all the grain with it hence the name full grain leather. This type of leather retains the inherent toughness, as well as the imperfections because there are no surface alterations or splitting
iii) Split leather - Corrected grain leather, also known as genuine leather, is produced using the skin layers that remain after the top is split off. Just like the top grain leather, it is also sanded to remove natural imperfections. Usually, the surface is spray painted and embossed with a leather-like pattern to resemble natural appearance. However, the processing alters the inherent breathability of the leather.
iv) Bonded leather - Bonded leather is made up of leftovers of the hide. This includes the dust and shavings. These are bonded together using polyurethane or latex on top of a fiber sheet. It is often spray-painted to look like full or top grain leather. You can’t determine the percentage of natural leather unless the manufacturer chooses to disclose it – which is very unlikely. Bonded leather is the lowest (and the cheapest) grade of leather.
Engraving Leather using Laser Machine
Laser processing is contact-free and produces consistent results without wear and tear.The laser beam melts the material and produces perfectly clean and sealed edges on the surface of the leather.
Advantages of laser technology
- Perfect sealed edges with laser cut leather
- Productive processing
- Non-contact processing
- Simple high-quality manufacturing
- One tool for all shapes
- No wear of the laser beam from material processing
This being the first time working with leather engraving, I selected a few pieces to work with and a design to test how to engrave it. Since I had earlier done a design for bat man I decided to use it for a test run for the engraving experiment. For me to be able to use it I changed the fill setting and put a black fill. I had used Inkscape to design the batman once down I printed it laser machine .
This is how it looks like in the engrave software so you select the laser side since we working with engraving. I put a Ratser power of 25%, Raster speed of 100% and a B/W Threshold of 5. The first test run and the results.
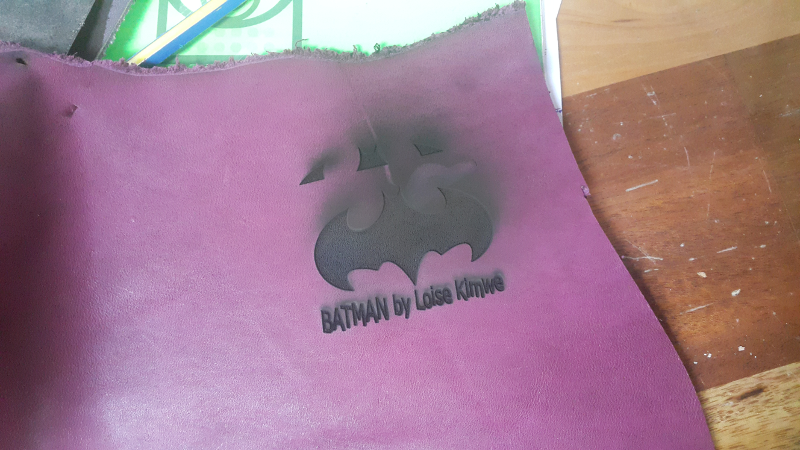
Using the following setting for several tests as shown.
Test 1
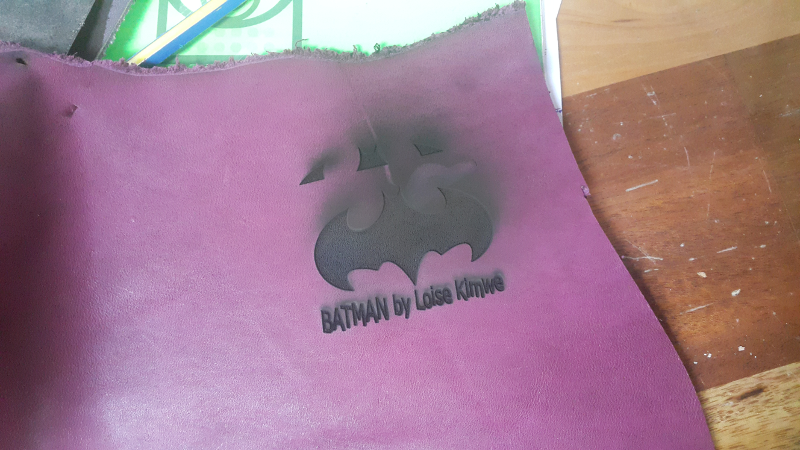
Test 2
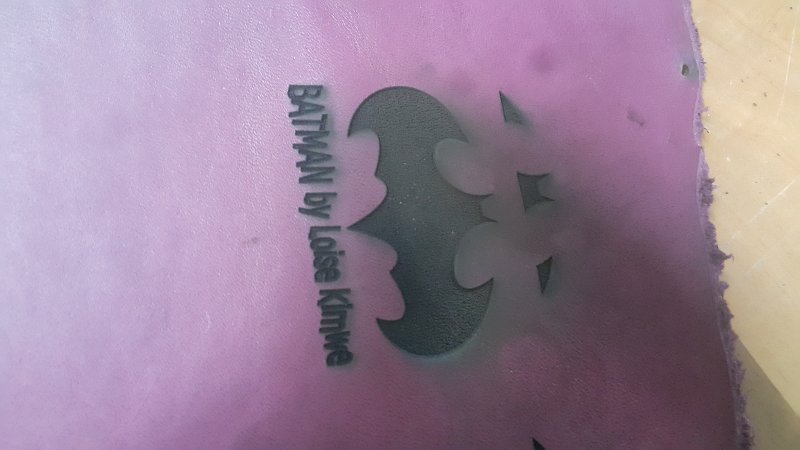
Test 3
This was the final test that I foud the correct settings for engraving the leather that I was using.
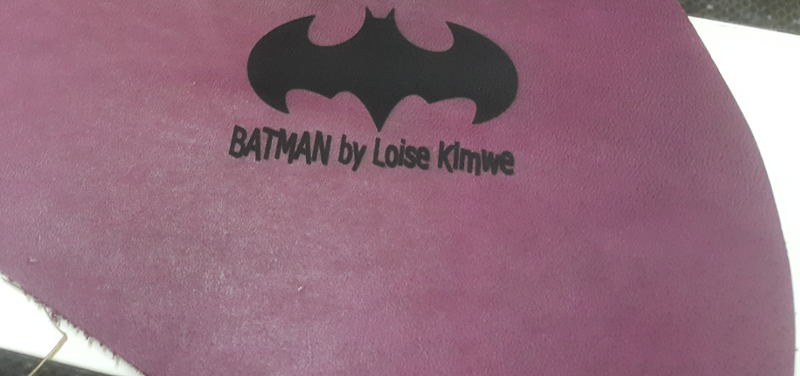
All the test in one leather piece.
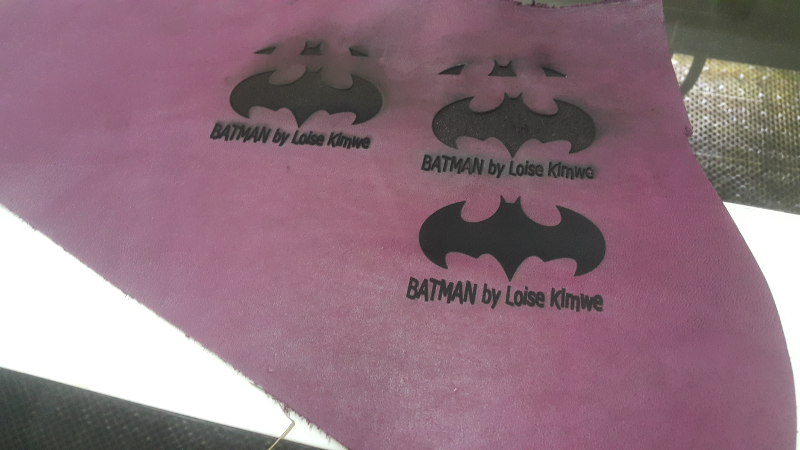
Challenges
The leather at first had an ash texture and the surrounding of the engaved image so I solved it by changing the settings.
Before
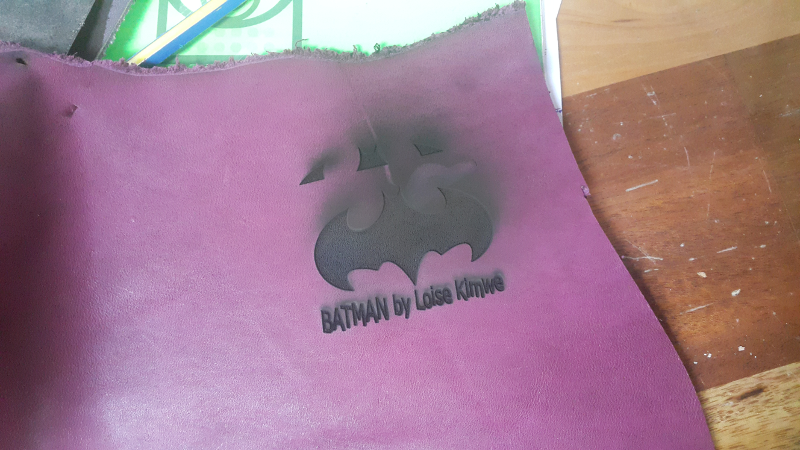
After
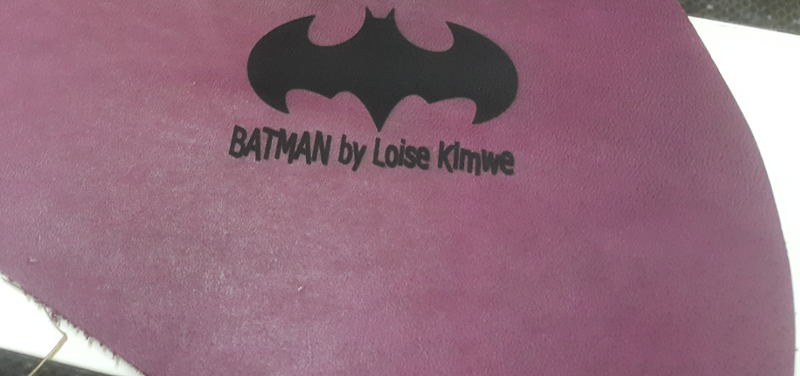
Engraving and Cutting Leather using Laser Machine
I really wanted to create something for everyone in the office so I decided to make keyholders with the logo and the name of the keyholder owner. I started with a simple design with the help of images from the internet. I used Inventor software to make the design using the drawing tools in the 2D sketch section as shown. I gave it dimensions based on the size that would be prefereable for a keyholder.
Then exported the file. Using inkscape I imported the design where I made changes by putting the logo and the name using the text tool and add png image button.
Once done I printed the design to the lasercutter machine using the RetinaEngrave3D software as shwon.
For rastering I selected the hafftone differ and put the settings for test 3 done above. The design has two parts the Raster and the vetor for the two to be differentiated I used different color fot the vector so that the laser machine can do one job at a time.
The below are the settings that I used for bot engraving a nd cutting out the leather piece.
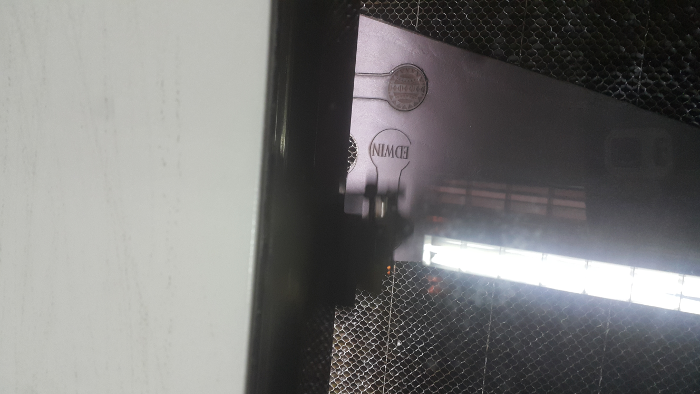
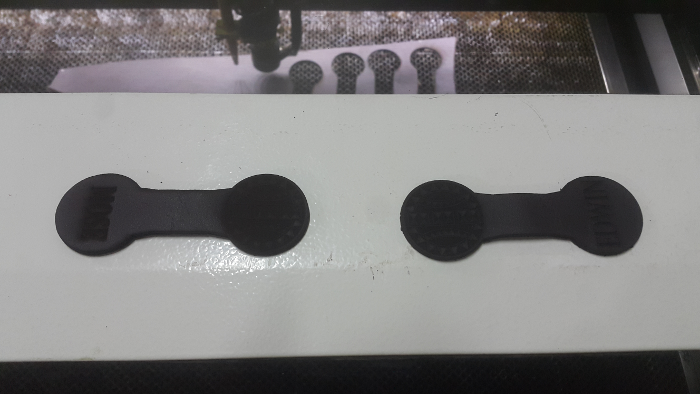
I used glue to join the two parts together.
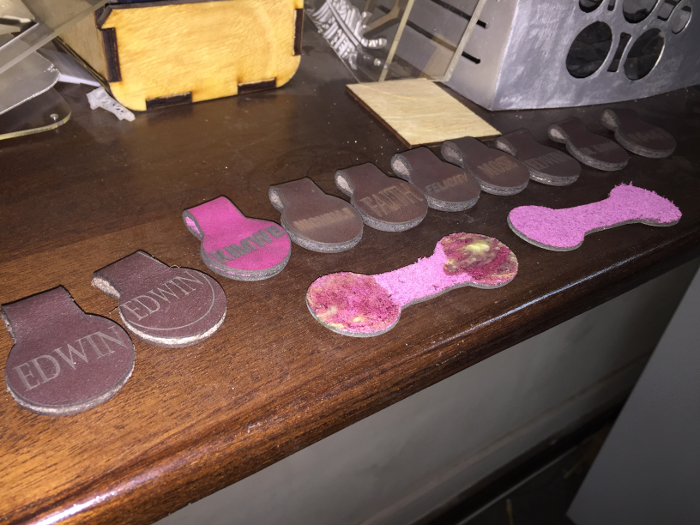
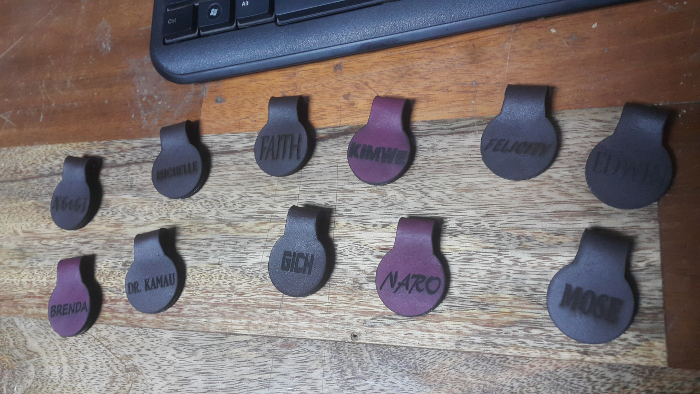
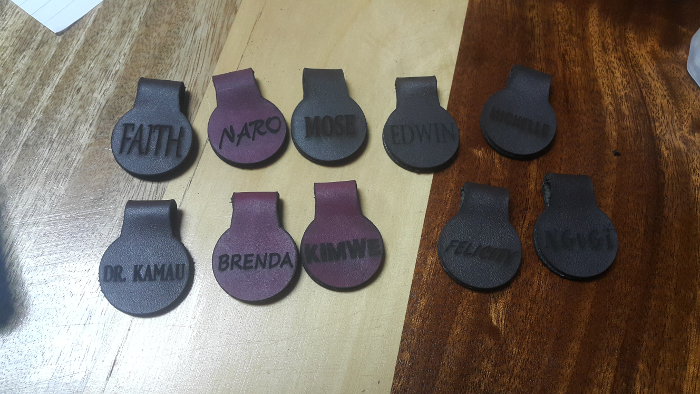
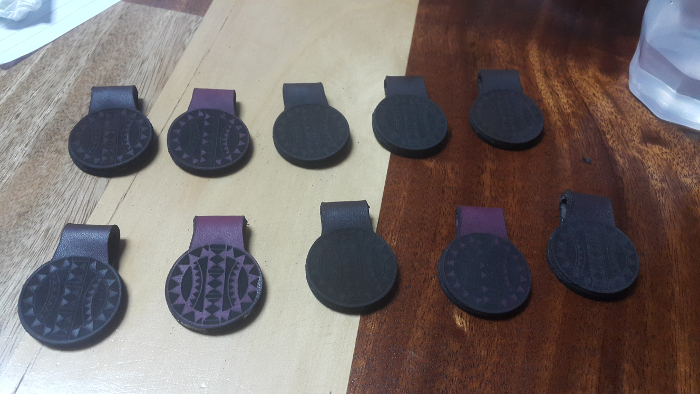
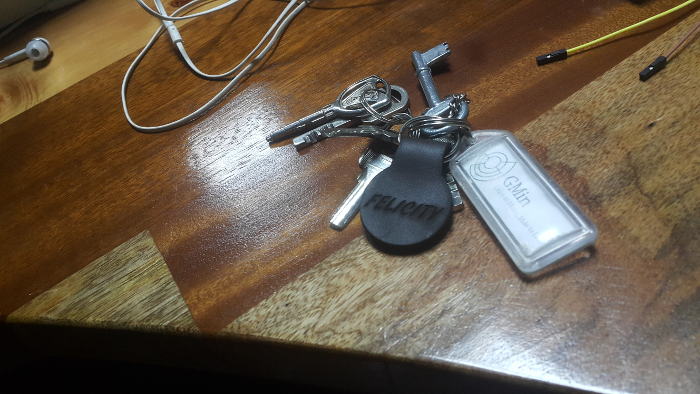
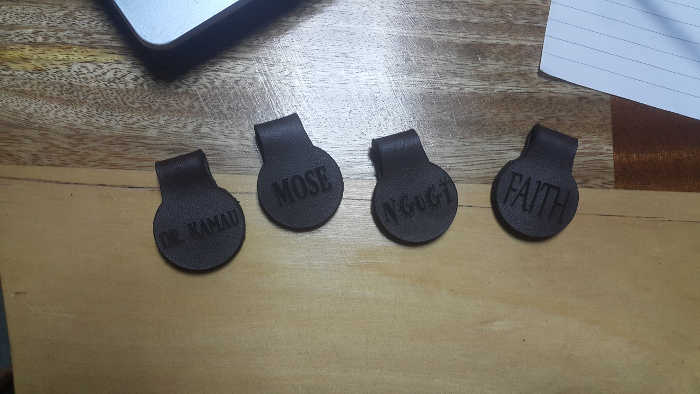
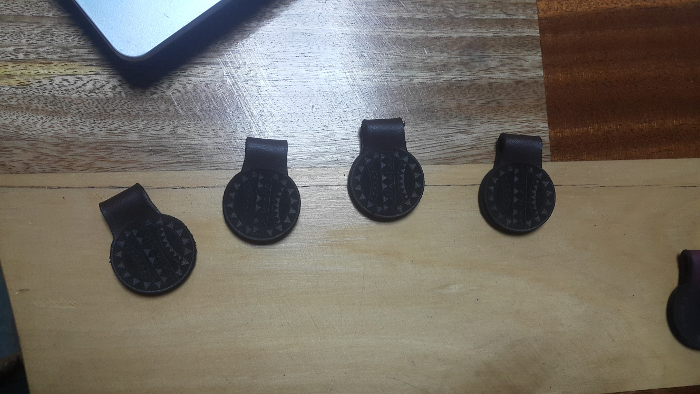